Die grinders are designed for grinding, sanding, honing, and polishing. They are mainly found in metal works and woodworking industries. The name die grinder is specified as the tool consists of dies and burrs, which help within the grinding process by making use of different tools. This information will discuss die grinders, their types, as well as their usage.
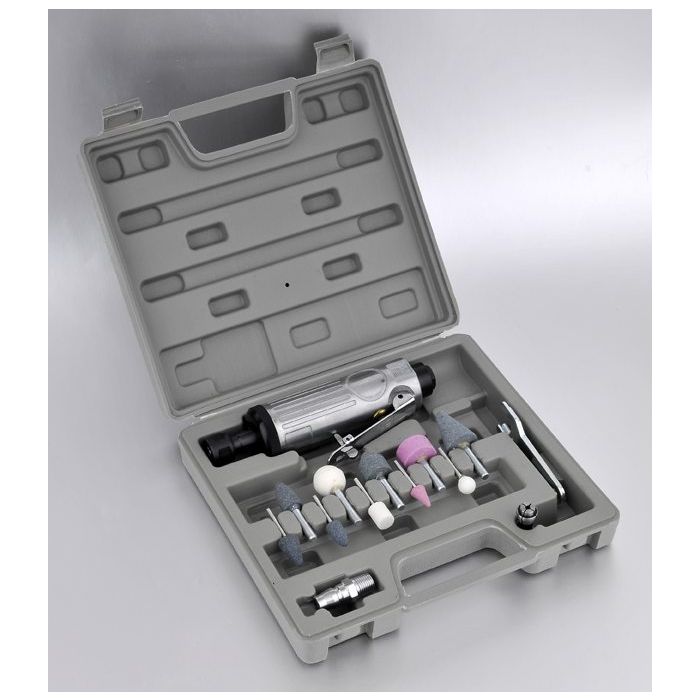
Die Grinder
A handheld power tool known as a die grinder is utilized for various cutting, grinding, sanding, honing, and polishing jobs. It truely does work with tiny abrasive attachments called “dies” or “burrs” with some other cutting and grinding tool shapes.
These are generally versatile machines utilized in various sectors, including metalworking, woodworking, automotive, and aerospace. People frequently propel die grinders by compressing air or electricity, websites as bad their small size and fast rotation, they may be suitable for precision work on delicate or small surfaces.
Machine operators, metal fabricators, and mechanics frequently use die grinders to grind and shape metal components, eliminate corrosion and rust, and tidy up welds, amongst other things.
What’s the Die Grinder’s Main system?
The operating system of a die grinder refers to what sort of tool functions along with the components that enable it to function. Die grinders may be operated by electricity or compressed air, and the range of os will depend on the applying and also the user’s preferences.
Electrically powered grinders are typically designed with a rotating shaft motor. The shaft is outfitted which has a collet that securely sports ths die or burr attachment available. The motor is generally run by a power cord connected a power outlet. Some models might also have a rechargeable battery that gives mobility and flexibility.
Conversely, compressed air-powered die grinders make use of a pneumatic system to work. The compressed air is towards the tool via a hose connected to a cloak compressor. Mid-air drives a turbine or vane motor that rotates the shaft within the tool. The collet is used to support the die or burr attachment set up.
Both electric and pneumatic die grinders use a trigger or switch that controls the tool’s speed and on/off functions. The velocity could be adjusted to accommodate the applying, plus some models could possibly have variable speed settings for really control. These most often have a top rotational speed, including 5,000 to 30,000 revolutions each minute (RPM), letting them quickly get rid of the material or perform precision develop small or intricate surfaces.
To conclude, the operating-system of the die grinder necessitates the automobiles, motor, collet, speed control, along with other components that enable the tool to function
Die Grinders Types
1. Pneumatic
This can be a handheld power tool powered by compressed air. It is also known as a cloak grinder or air-powered grinder. The tool converts compressed air into mechanical energy through a high-speed motor system that rotates a spindle. The spindle is fitted which has a collet that securely holds various attachments, including grinding wheels, sanding discs, and polishing pads.
Pneumatic die grinders are traditionally used in industrial and manufacturing settings requiring high torque and speed. These are frequently used for grinding, sanding, polishing, and cutting applications and therefore are especially ideal for precision focus on small or intricate surfaces.
One of the primary attributes of pneumatic die grinders is power-to-weight ratio. These are typically lighter and much more compact than electric models, yet they could produce higher speeds and greater torque. Additionally, pneumatic die grinders are less inclined to overheat, which makes them ideal for prolonged use in demanding environments.
A way to obtain compressed air is necessary to operate pneumatic die grinders. The tool is associated with an aura hose that come with a compressor or another compressed air source. Air supply is controlled by a trigger or valve on the tool, that enables the user to control the rate and power of the grinder.
2. Electric
An electric die grinder can be a handheld saw run by electricity. It is usually known as an electric or corded rotary tool. The tool converts electric power into mechanical energy through a motor system that rotates a spindle at high-speed. The spindle is suited having a collet that securely holds various attachments, including grinding wheels, sanding discs, and polishing pads.
They are traditionally used in several industries, including woodworking, metalworking, and automotive. They’re frequently used for grinding, sanding, polishing, and cutting applications and therefore are especially useful for precision focus on small or intricate surfaces.
One of the first features of electric die grinders could be the simplicity of use. They require no external air supply and could be used virtually anywhere a power outlet exists. Electric die grinders are typically quieter than pneumatic models and could offer more consistent performance, even though they are generally less powerful.
The tool is attached to a local store using an electric cord to operate an electrical die grinder. A variable-speed dial controls the pace and power the grinder or triggers around the tool, that enables an individual to alter the velocity and torque according to the application. Overall, these grinders are versatile, efficient, and reliable tools traditionally used in lots of industries.
Uses
Die grinders are extremely versatile saws and could be utilized for a variety of applications. A number of the common reasons like die grinders include:
Grinding: Die grinders are fantastic for grinding & giving shape to metal, wood, & other materials. They are often accustomed to lessen welds, remove rust or paint, and make preparations surfaces for further finishing.
Sanding: They can sand wood, metal, along with other surfaces. These are very theraputic for sanding intricate or hard-to-reach areas.
Polishing: They are often fitted with polishing pads and used to polish metal, stone, as well as other materials. They are ideal for buffing out scratches, blemishes, as well as other imperfections.
Cutting: They are often employed for cutting a variety of materials, including metal, wood, and plastic. They are handy for cutting in tight spaces or making precise cuts.
Engraving: They can be fitted with carbide burrs or any other attachments and used for engraving metal, wood, along with other materials. They are ideal for creating detailed designs or etchings.
Deburring: They’re able to remove burrs and sharp edges from metal, plastic, and other materials. They are ideal for cleaning rough or uneven edges after cutting or grinding.
These are flexible, effective instruments frequently used in several fields, including metalworking, woodworking, automotive, and construction.
Conclusion
To sum everything up, die grinders are powerful and versatile tools which you can use for various applications in numerous industries. Electric die grinders and pneumatic grinders include the two main types out there, each using its advantages and drawbacks.
Both grinders are helpful for grinding, sanding, polishing, cutting, engraving, and deburring various materials, including metal, wood, plastic, plus more. With the proper attachments and accessories, die grinders can be customized for particular applications, which makes them valuable to the professional or DIY toolbox.
For more details about 1 4 die air grinder accessories air take a look at our new resource